Drive-in Pallet Racks
Drive-in pallet rack systems offer high-density storage for multiple units of the same product. The drive in system is an alternative to push back racking that is comprised of lanes where the bottom pallets rest on the floor and the upper pallet levels rest on support rails. Each storage lane may be 2 to 10 pallet positions deep. Each storage lane must be wide enough to drive the forklift in between the support rails. Forklifts travel in the lanes with the loads elevated at the selected storage level. Unit load rotation for drive-in pallet rack systems is last in, first out (LIFO). In a drive-in rack system the forklift enters into the lane going forward and backs out to exit the lane.
Before Drive-In
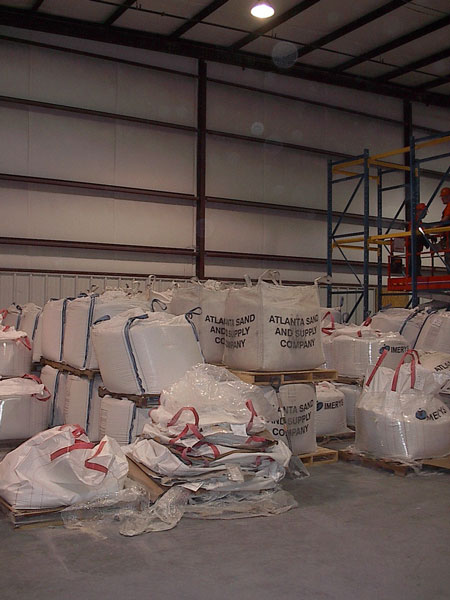
After Drive-In
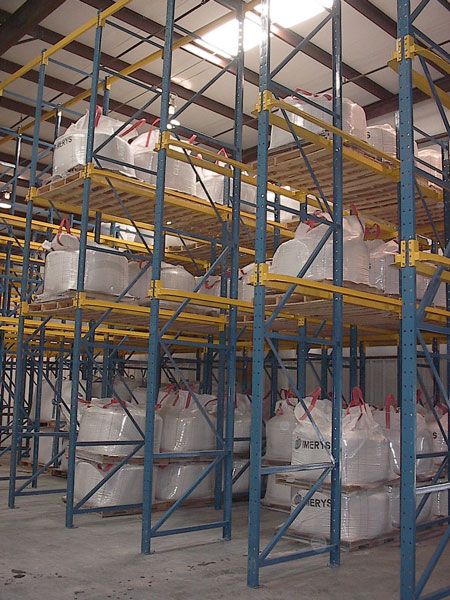
Drive-In Utilization
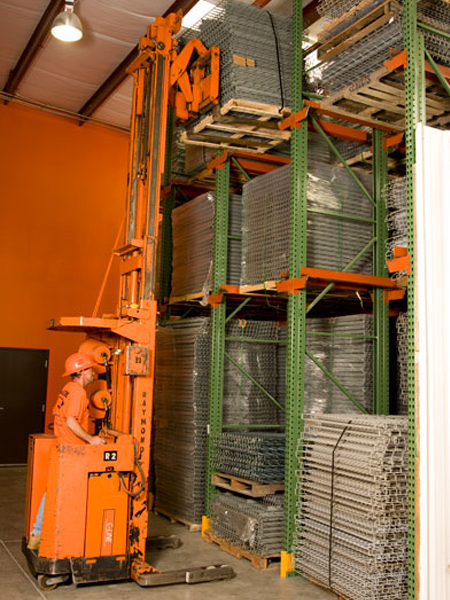
Drive Through
The difference between drive-in and drive-through (also sometimes spelled Drive-thru) racking systems is that drive-in pallet racking systems have one entry, which the forklift must drive in and back out of. In Drive-through racking systems there are two entries per lane, which the forklift can enter and exit through. Drive through rack systems are similar to drive in rack systems except there are no back brace beams. In drive through rack systems each storage lane is accessible from two aisles. A drive through storage system with two different entry points can use first in, first out (FIFO) unit load rotation or last in, first out (LIFO) unit load rotation. With a FIFO unit load rotation, pallets are loaded into the entry side and pulled from the exit side. The first placed in the row is the first pallet taken out at the other end. This system is advantageous for material with an expiration date, where stock rotation is a major concern. Drive-in/Drive-through pallet rack systems can be built in both roll form and structural steel, for heavy duty applications structural steel construction is preferred.